Cement Silo Unblocking
Introduction
A cement plant with a relatively old silo system required the emptying of an overfill cement silo. The overfill cement silo formed by the connection of four silos had not been used in several years. This resulted in the caking of the cement and therefore blocking its discharge system.
Work Performed
- Modification of the existing discharge duct section
- Installation of a new discharge duct
- Unblocking and discharging the overfill silo
Scope
A cement manufacturing company engaged Talos General Construction to work at its overfill silo which had not been in use for several years. Since the cement silo had not been in use for years, the discharge system was blocked with caked cement. This overfill silo is formed when four are connected and act as a safety feature in case of an overfill of any one of the 4 primary silos.
The client required the secondary silo to be emptied, to maintain its function at the plant and to also pack cement for selling.
Access
The silos were constructed on piles and they were elevators from the ground to create a bunker where the discharge system was with a screw system that transfers material to the packing plant. Using the access doors underneath the silo, Talos’ technicians were able to reach the discharge area of the overfill
silo.
Solution
The first stage of services for this client was to check the level of the cement inside the silo and estimate the amount of silo that could be extracted from the silo. After the estimation of tonnage, Talos Group checked the type of discharge system used on this silo. Subsequently, a method statement was derived and the best solution was to modify the discharge system to unblock the base port safely and avoid spillages.
Ball valves were installed on the discharge duct to act as access inside the silo. The access created is for inserting hammer drills with various lengths to
break the solidified material.
In case of an overflow of soft material, the ball valve (control valve) will be closed to avoid spillage and engulfment of cement. The diameter of the valve had to be almost the same size will the drill bits to minimize the opening while the drill is inside. A control mechanism was required to allow the technicians to avoid uncontrollable spillage.
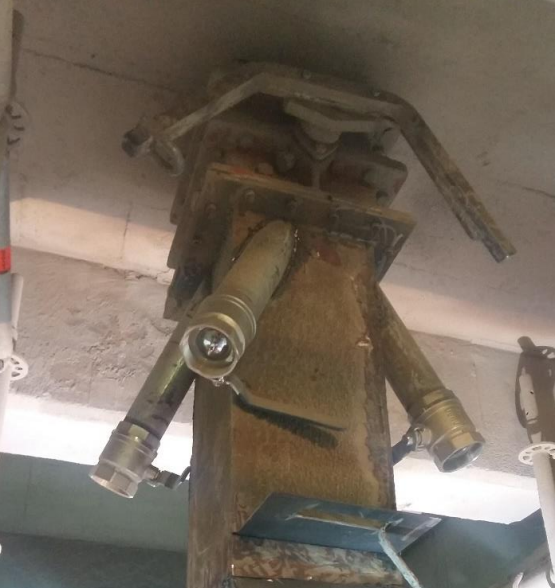
Since the client wanted to pack the soft/fine cement, the second stage was to modify the discharge duct itself and install a sieve and hatch to remove the large lumps of solidified material.
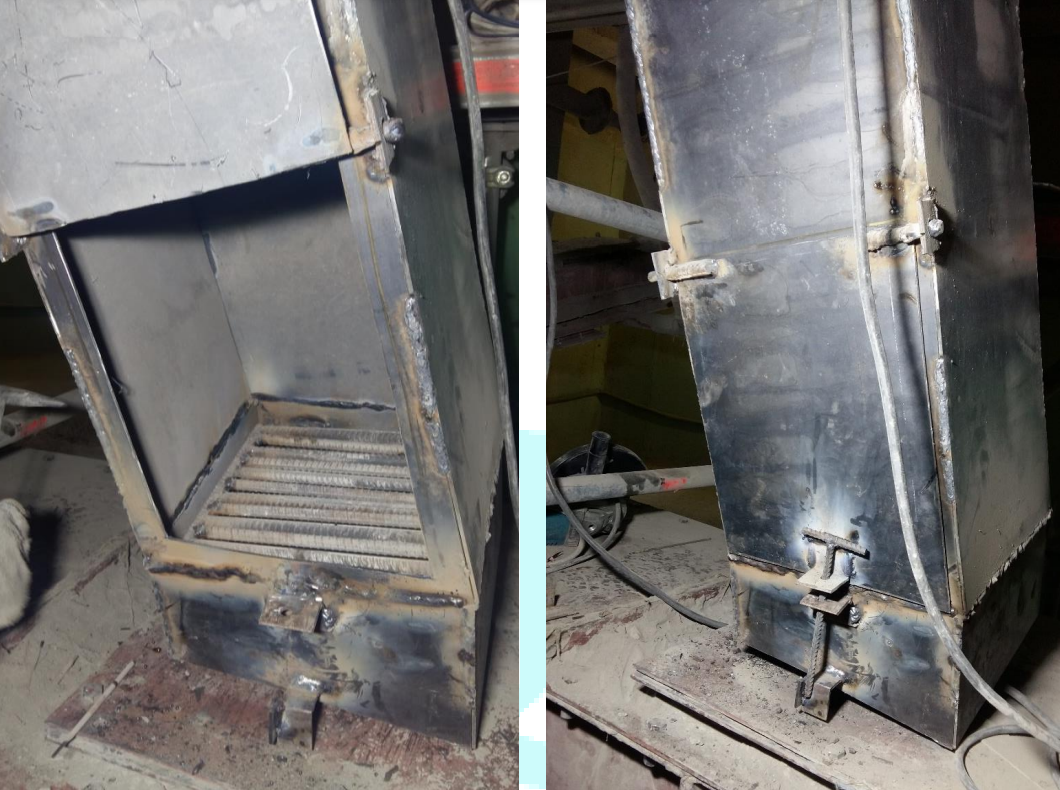
Figure 2: Modified discharge duct with sieve and hatch
Results
The discharge of the overfill silo work was completed safely and successfully. Regular checks of the silo
levels and timely emptying of the silo are crucial to prevent caking and overfilling of cement silo. The silo
should maintain its intended functionality to ensure safety.